锂电池结构件精密加工产业链:动力电池精密结构件
动力电池精密结构件,广义来讲包括电芯顶盖、钢/铝外壳、正负极软连接、电池软连接排等,狭义来讲主要包括电芯壳体和顶盖,对锂电池的安全性、密闭性、能源使用效率等都具有直接影响。按照电池封装技术路线的不同,主要有方形、圆柱、软包三种形状,对应的结构件分别为方形结构件、圆柱结构件和铝塑膜。
整体来看,圆柱和方形统称为硬壳,封装结构较为相似,均由壳体和盖板组成。软包电池封装较为特殊,由铝塑膜构成。
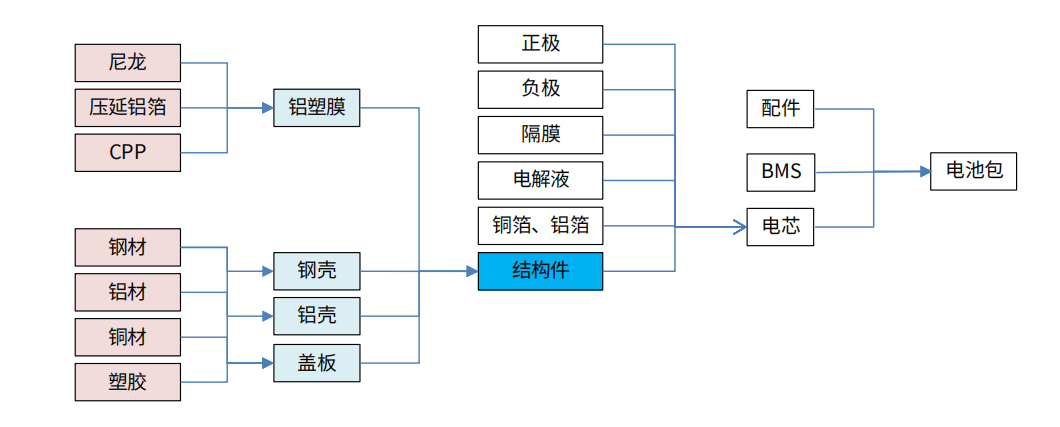
图为锂电池结构件产业链图解
工艺端:精密制造
盖板的主要生产工艺包括冲压、焊接、注塑等,壳体的生产工艺主要是冲压、拉 伸。铝塑膜的主要生产工艺包括精密涂布、贴合等。
图为铝塑膜流程
对结构件的需求来自于电池封装。目前,主流的电池封装技术主要有方形电池、圆形电池以及软包电池三类。动力电池的安全性和使用寿命都受其封装工艺的影响,不同的封装技术都具有不同的技术壁垒。封装工艺设计除需满足耐撞击振动和挤压穿刺的物理冲击外,也需满足防火阻燃等化学性能要求。
图为不同封装技术电池结构
硬壳结构件:盖帽是关键,防爆片铝材有待降本
硬壳结构件包括圆柱和方形结构件,通常由壳体和盖板组成。其中,盖板的制造工艺复杂度通常远高于壳体。
盖板
盖板的主要功能包括:
1)固定/密封功能:顶盖与铝壳激光焊接,包裹固定裸电芯并实现密封作用;
2)电流导通功能(极柱):在电池中,顶盖极柱、转接片和电芯极耳焊接导通,保证电芯充放电电流导通的功能;在模组中,顶盖极柱与汇流排激光焊接、螺栓连接,形成串/并联;
3)泄压功能(防爆片):当电池出现异常,内部气压增大至一定值,顶盖防爆阀将开启进行泄压,降低爆炸风险;
4)熔断保护功能(翻转片):当电池出现异常,内部气压增大至一定值,顶盖翻转片向上顶起,与负极铆接块接触,使顶盖正负极直接短路,同时铝连接片Fuse熔断,快速切断电流;
5)降低电腐蚀:正极上塑胶采用导电PPS,保证正极柱与顶盖板间有一定阻值,降低正极柱与铝壳间的电位差,防止顶盖板/铝壳电腐蚀,进而提高产品质量和使用寿命
盖板中重要部件主要有:
1)防爆片:一般磷酸铁锂体系电池顶盖采用单个防爆阀设计,防爆阀开启压力一般为0.4~0.8MPa。当内部压强增大并超过防爆阀的开启压力时,防爆阀将从刻痕处破裂并开启进行泄压;
2)翻转片:三元体系电池除了采用防爆阀外,还会叠加SSD翻转片组合设计形式,防爆阀开启压力和SSD翻转压力一般分别为0.75~1.05MPa、0.45~0.5MPa。当电池内部压强增大至SSD 翻转压力时,翻转片向上顶起,快速切断电流;
3)极柱:主要是起到电流导通作用。通常正极采用铝极柱,负极采用铜铝复合极柱。
壳体
壳体的制造相对简单,主要采用连续拉伸工艺。由于盖板集成部件较多,工艺较为复杂,且在实际作用时,防爆阀开启后电解液容易飞溅至盖板接线造成二次事故,因此出现了将防爆阀转移至壳体的现象。
铝塑膜:国产替代进行时
与圆柱、方形电池的硬壳不同,软包电池采用铝塑膜封装。铝塑膜由铝箔、多种塑料和粘合剂(包括粘接性树脂)组成,按照制作工艺区分,主要有干法和热法两种。相比热法铝塑膜,干法铝塑膜更加适用于大倍率、高能量动力电池,应用更加普遍。
因为与电池的内部材料直接连在一起,所以电解液会浸润到铝塑膜的内层,故要求其具备以下性能:
1)极高的阻隔性;2)良好的热封性能;3)内层材料耐电解液及强酸,不与电解液反应;4)良好的延展性、柔韧性和机械强度。
在结构上,铝塑膜为一种三层膜的复合材料,主要由尼龙层(ON)、铝箔层(AL)、流延或未拉伸聚丙烯层(CPP)相互粘合后构成。根据铝塑膜厚度的不同,可分为88μm、113μm、152μm,其中厚度152μm的铝塑膜适用于动力电池,而更薄的88μm和113μm适用于3C领域。
图为铝塑膜结构示意图
在成本上,铝塑膜占到整只电芯的18%,仅次于正极(30%)和电解液(25%),属于占比较大的一种成分。在铝塑膜本身的构成中,铝箔的成本占到65%。在铝塑膜的原材料中,铝箔是核心材料,厚度5-9μm,国内产能较丰富,领先的压延铝箔企业包括华西铝业、渤海铝业、河南神马等,但国内产品在性能方面不及国际产品,主要供应中低端3C消费电子领域。CPP(流延聚丙烯薄膜)主要起到封口作用,国内生产企业主要有佛塑科技、广东仕诚、佛山俊嘉等,但产品主要用于低端3C消费电子领域。BOPA(双向拉伸尼龙薄膜)位于最外层,主要起到保护作用。国内厂家主要有沧州明珠、佛塑科技、厦门长塑等,但主要应用领域为3C消费电子领域。综上,国内原材料主要应用于3C消费电子领域,在软包动力电池领域所需原材料仍依赖进口。
图片
图为铝塑膜产业链示意图
动力电池模组连接片焊接方式
新能源动力锂电池
新能源汽车需要使用锂电池作为动力电池。动力电池即为工具提供动力来源的电源,多指为电动汽车、电动列车、电动自行车、高尔夫球车提供动力的蓄电池。其主要区别于用于汽车发动机起动的起动电池。
动力电池作为新能源汽车的核心零部件,其用来导电连接的配置就是其重中之重。动力电池电芯单体与模组母排之间的连接方式,不仅影响动力电池的制造效率,还决定动力电池生产是否可以实现自动化,其对动力电池模组装车以后的性能表现同样有不容忽视的影响。
动力电池模组连接片
动力电池模块的连接片大多采用多层材料复合材料的方法,其中一层材料是连接件和极柱之间的连接层,以保证焊接性能。采用多层材料叠加,保证连接片的导电性。
连接板基板经过多层箔堆叠后加工成型,可形成柔性区域,用于补偿动力电池芯部膨胀引起的位移,减小对低强度界面的影响。
铜软连接
动力电池模块的连接件一般为矩形、梯形、三角形、台形,连接面粘贴0.1厚的镀镍铜箔,焊接时表面在高温下容易氧化变色,并在不破坏产品表面涂层的情况下进行抛光清洗。这样的产品不仅解决了整体电镀的问题,还解决了电导率最大化的问题。
铜镀镍连接片最好,其次纯镍连接片,可是价格偏贵,最后是镀镍钢连接片,镀镍钢连接片价格相对便宜,并容易焊接。
各动力电池生产商选用连接片的厚度是不同的,因连接片的厚度关系到耗用材料的重量及整体动力电池模组的重量,降低厚度是动力电池模组向轻量化设计的方向。
铝软连接
动力电池模组常用的汇流排有:镍片、铜铝复合汇流排、铜汇流排、总正总负汇流排、铝汇流排,铜软连接、铝软连接、铜箔软连接等。
动力电池模组连接的焊接方法
动力电池电芯单体与模组母排之间的连接方式,不仅影响动力电池的制造效率,还决定动力电池生产是否可以实现自动化,其对动力电池模组装车以后的性能表现同样有不容忽视的影响。
应用于动力电池模组连接的焊接方法主要有:
1.电阻焊
电阻焊是一种以电阻热为能量的焊接方法。电阻焊是利用电流流过工件接触面和相邻区域产生的电阻热效应,将其加热到熔融或塑性状态,同时加压形成金属结合。
电阻焊焊接时不需要填充金属,生产率高,焊件变形小,易于自动化。为了防止接触面上的电弧和锻焊金属,焊接时应始终施加压力。在电阻焊接过程中,待焊接工件的接触表面对于获得稳定的焊接质量至关重要。因此,在焊接之前,必须清洁电极和工件之间以及工件之间的接触表面。
在动力电池的分组工艺中,电阻焊是比较成熟的工艺,应用于动力电池连接片与汇流条的焊接,动力电池极与并联导电条的连接等。
由于其设备简单、成本低廉,在动力电池行业发展初期得到了广泛应用。近年来逐渐被更先进的激光焊接和高分子扩散焊所取代。
2.激光焊
激光焊接效率高,易于实现自动化生产。在不断改进焊接工艺,限制成型过程中的热影响以后,在实际生产中的应用也越来越多,激光焊接配合工业机器人正在逐步成为自动化动力电池模组生产线的主力。
激光焊接
激光焊接是利用高能量密度的激光束作为热源的一种高效精密焊接方法,激光焊接主要用于焊接薄壁材料和低速焊接,激光焊接过程属热传导型,即激光辐射加热工件表面,表面热量通过热传导向内部扩散,通过控制激光脉冲的宽度、能量、峰值功率和重复频率等参数,使工件熔化,形成特定的熔池。
3.高分子扩散焊
高分子扩散焊是新一代的扩散焊机, 导电带软连接设备,主要由主机与控制两部分组成,可实现高分子材料间的扩散焊接广泛应用于电力、化工、冶炼等行业,主要生产行业急需的母线伸缩节和软连接导电带产品,可实现软母线、软母线与硬母线、硬母线之间的扩散焊接。
其原理就是在一定温度和压力下,将待焊物质的焊接表面相互接触,通过微观塑性变形或通过焊接面产生微量液相而扩大待焊表面的物理接触,使之距离达(1~5)×10-8cm以内(这样原子间的引力起作用,才可能形成金属键),再经较长时间的原子相互间的不断扩散,相互渗透,实现冶金结合的一种焊接方法。
高分子扩散焊是一种特殊的焊接工艺,能使用不同强度的铜箔在特定的区域焊接在一起,这种焊接工艺不需要使用任何形式的助焊剂,可实现完美的分子连接性,主要用于动力电池的软连接。安装接触面可以承受任何形式的挤压、弯曲、或者碰撞。由于安装接触面是定制的,所以它可以安装到只有2mm的空间内。
对于新能源汽车电池模组连接片的焊接来说,高分子这项工艺不需要焊料,就可以实现焊接,且焊接后质量合格,外观平整精美。且高分子扩散焊机采用高频变压器,电压低,从而可以有效降低了由高压引起的绝缘和打火问题,增强了设备的可靠性。
锂电池盖帽工作原理
一、电池盖帽的作用与原理
(1)正或负极引出端
(2)温度保护作用:PTC (电阻骤增,切断电流)
(3)断电保护功能:CID 电流断开装置
(内压上升→Vent翻转→CID焊点拉断)
(4)泄压保护功能:Vent
(内压上升→Vent翻转→CID焊点拉断→压力持续上升→ Vent破裂)
(5)密封功能:防水、气入侵、防电解液蒸发
二、盖帽的保护机制
(1)正常状态
(2)CID 断裂和Vent翻转
(3)Vent 破裂
三、盖帽压力设计
(1)内部压力推动 vent 翻转
(2)Vent 翻转拉断 CID 焊点
(3)控制点: (1) vent 翻转压力,(2) CID 焊点拉力
CID 断开压力 =Vent 翻转压力+ CID焊点拉力的等效压力
CID焊点拉力转换为等效压力:CID焊点拉力的等效压力(MPa)=CID 焊点拉力(N)/78.5
四、盖帽翻转示例
监控增加压力后vent 翻转高度;Vent 在 0.75MPa 翻转。
4.1 下图Vent翻转压力和高度数据关系图
4.2 下图为Vent翻转后的实物照片
4.3 Vent 翻转高度的检验示意图
五、盖帽拉断与翻转关系
2.1 CID 焊接拉力希望越小越好?
对 Vent 翻转影响小
2.2 焊接拉力太小可能出现的问题?
振动导致CID焊点断开,然而CID 重量约0.1g, 0.1N 焊接拉力能抵抗100G 振动,因此我们可以忽略它的影响。
六、 焊接拉力对CID影响
实验数据表明焊接拉力在[16N,32N ],对应CID断开压力在[ 0.2MPa,0.4MPa]。说明焊接拉力对CID 断开影响较小, CID断开主要与Vent 翻转压力关系较大。
七、盖帽设计要点
(1)减小盖帽高度
(2)Vent双面刻痕优化为单面刻痕,Vent的爆破翻转一致性更好
(3)利用硬铝CID应用,Vent刻痕不易拉伸变形其爆破一致性更好
版权声明:除原创内容及特别说明之外,推送稿件文字及图片均来自网络及各大 主流媒体。版权归原作者所有。如认为内容侵权,请联系我们删除。
精密加工//chuanchuanjiqi.cn/