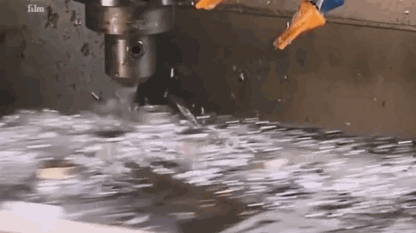
刀具崩刃的原因及对策
1)刀片牌号、规格选择不当,如刀片的厚度太薄或粗加工时选用了太硬太脆的牌号。
对策:增大刀片厚度或将刀片立装,选用抗弯强度及韧性较高的牌号。
2)刀具几何参数选择不当(如前后角过大等)。
对策:可从以下几方面着手重新设计刀具。 适当减小前、后角。 采用较大的负刃倾角。 减小主偏角。 采用较大的负倒棱或刃口圆弧。 修磨过渡切削刃,增强刀尖。
3)刀片的焊接工艺不正确,造成焊接应力过大或焊接裂缝。
对策:避免采用三面封闭的刀片槽结构。正确选用焊料。避免采用氧炔焰加热焊接,并且在焊接后应保温,以消除内应力。尽可能改用机械夹固的结构
4)刃磨方法不当,造成磨削应力及磨削裂纹;对PCBN铣刀刃磨后刀齿的振摆过大,使个别刀齿负荷过重,也会造成打刀。
对策:采用间断磨削或金刚石砂轮磨削。选用较软的砂轮,并经常修整保持砂轮锋利。注意刃磨质量,严格控制铣刀刀齿的振摆量。
5)切削用量选择不合理,如用量过大,便机床闷车;断续切削时,切削速度过高,进给量过大,毛坯余量不均匀时,切削深度过小;切削高锰钢等加工硬化倾向大的材料时,进给量过小等。
对策:重新选择切削用量。
6)机械夹固式刀具的刀槽底面不平整或刀片伸出过长等结构上的原因。
对策:修整刀槽底面。合理布置切削液喷嘴的位置。淬硬刀杆在刀片下面增加硬质合金垫片。
7)刀具磨损过度。
对策:及时换刀或更换切削刃。
8)切削液流量不足或加注方法不正确,造成刀片骤热而裂损。
对策: 加大切削液的流量。 合理布置切削液喷嘴的位置。 采用有效的冷却方法如喷雾冷却等提高冷却效果。 采用*切削减小对刀片的冲击。
9)刀具安装不正确,如:切断车刀安装过高或过低;端面铣刀采用了不对称顺铣等。
对策:重新安装刀具。
10)工艺系统刚性太差,造成切削振动过大。
对策: 增加工件的辅助支承,提高工件装夹刚性。 减小刀具的悬伸长度。 适当减小刀具的后角。 采用其它的消振措施。
11)操作不慎,如:刀具由工件中间切入时,动作过猛;尚未退刀,即行停车。
对策:注意操作方法。
撞机的原因归纳起来大概有9点
1)程序编写错误。
工艺安排错误,工序承接关系考虑不周详,参数设定错误。
A. 坐标设定为底为零,而实际中却以顶为0;
B. 安全高度过低,导致刀具不能完全抬出工件;
C. 二次开粗余量比前一把刀少;
D. 程序写完之后应对程序之路径进行分析检查。
2)程序单备注错误。
A.单边碰数写成四边分中;
B.台钳夹持距离或工件凸出距离标注错误;
C.刀具伸出长度备注不详或错误时导致撞刀;
D.程序单应尽量详细;
E.程序单设变时应采用以新换旧之原则:将旧的程序单消毁。
3)刀具测量错误。
A.对刀数据输入未考虑对刀杆;
B.刀具装刀过短;
C.刀具测量要使用科学的方法,尽可能用较精确的仪器;
D.装刀长度要比实际深度长出2~5mm。
4)程序传输错误。
A.程序号呼叫错误或程序有修改,但仍然用旧的程序进行加工;
B.现场加工者必须在加工前检查程序的详细数据;
例如程序编写的时间和日期,并用熊族模拟。
5)选刀错误。
6)毛坯超出预期,毛坯过大与程序设定之毛坯不相符。
7)工件材料本身有缺陷或硬度过高。
8)装夹因素,垫块干涉而程序中未考虑。
9)机床故障,突然断电,雷击导致撞刀等。
CNC加工中心数控机床作为高精度的机床,防撞是非常必要的,要求操作者养成认真细心谨慎的习惯,按正确的方法操作机床,减少机床撞刀现象发生。有人说:曾经有一份工作在我面前,直到我撞机了。你撞过吗?来分享分享啥感觉啊?
关键词:南京9游服务精密科技有限公司,主营:南京精密加工公司,南京CNC加工,南京医疗器械精密零件,南京机器人精密零件,南京无人机精密零件,南京汽车精密零件,南京医疗设备精密零件,南京光学精密零件,南京精密加工chuanchuanjiqi.cn